Industry-Focused Cleaning Strategies for Professional Results
Maintaining spotless, compliant workspaces isn’t just about appearance; it’s about safety, efficiency, and cost control. Across sectors from agriculture to hospitality, a tailored approach to cleaning can simplify inventory, reduce waste, and keep operations running smoothly. Below, we explore the common challenges in various industries and outline practical techniques for achieving consistent, eco‑friendly results.
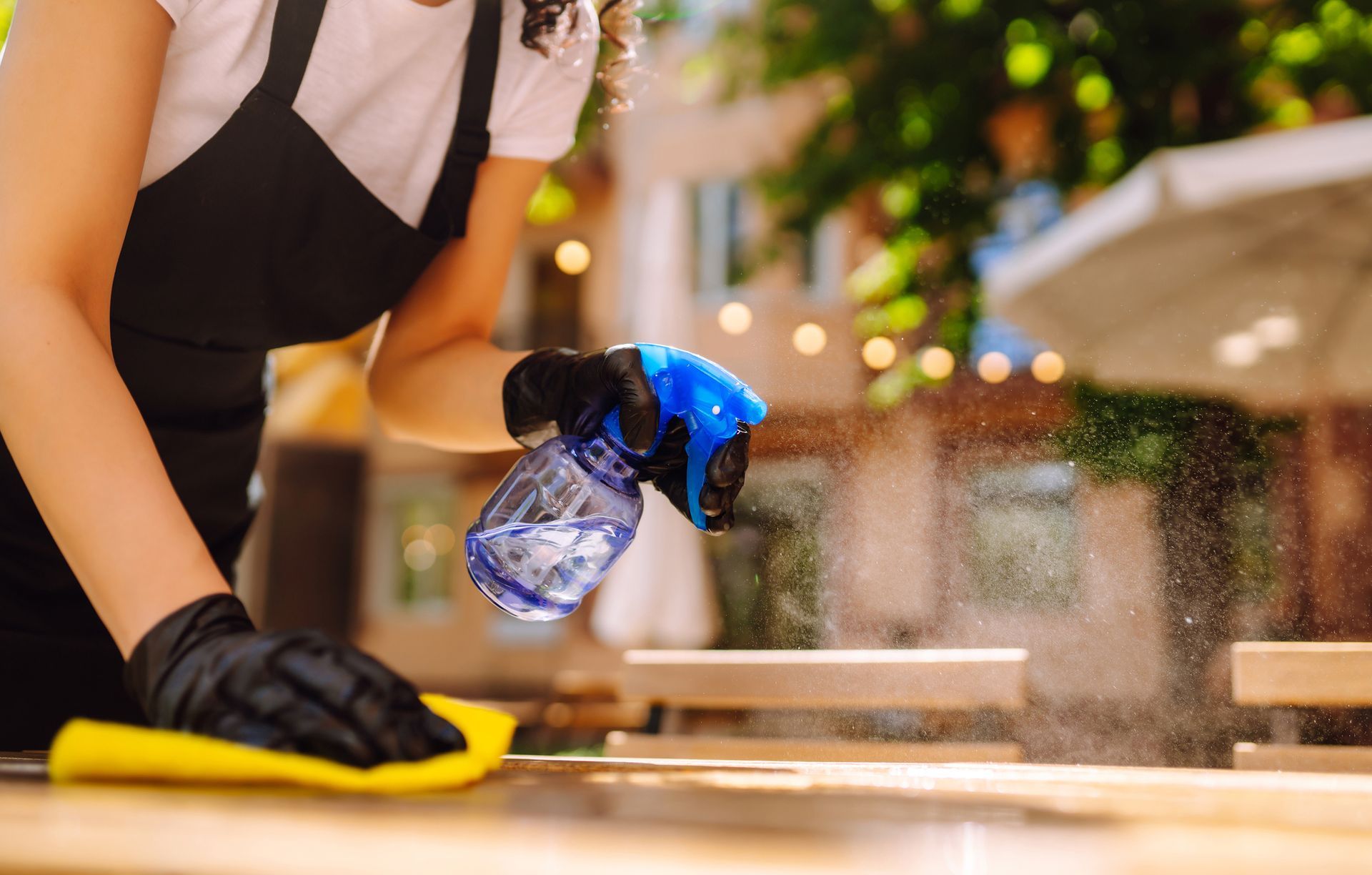
Why an All‑in‑One, Biodegradable Cleaner Makes Sense
- Simplified inventory: One concentrated formula replaces multiple specialty chemicals, reducing storage space and training time.
- Environmental responsibility: A 100% rapidly-biodegradable solution minimizes runoff impact and aligns with sustainability goals.
- Cost efficiency: Bulk purchasing and reduced product overlap help lower overall supply expenses.
Agriculture
Key challenges: grease, mud, organic residues, and variable water temperatures.
- Deep‑rooted cleaning: Use a high‑emulsion formula that penetrates thick soils on tractors, harvesters, and barn floors.
- Cold‑water activation: Choose a product that maintains performance in cool or fluctuating temperatures to accommodate early‑morning field wash‑downs.
- Residue‑free rinse: Ensure no film is left behind on food‑contact surfaces or milking equipment.
Automotive
Key challenges: oil, brake dust, carbon buildup, and incompatible surface materials.
- Degreasing strength: Opt for surfactants designed to lift hydrocarbons without harsh solvents.
- Multi‑surface compatibility: Verify that panels, upholstery, plastics, and painted finishes aren’t damaged by the cleaner.
- Frequent‑use safety: Select low‑fume, non‑abrasive chemistries to protect technicians during repeated applications.
Retail
Key challenges: high foot traffic, glass smudges, changing room upkeep, and fast turnaround between customers.
- Streak‑free shine: Incorporate a neutral‑pH glass and surface cleaner component to maintain a polished look on doors, counters, and displays.
- Quick‑dry formulation: Accelerate floor‑care routines with fast‑evaporating agents that minimize slip hazards.
- Versatile dilution: Use adjustable concentration for light touch‑ups versus deep cleaning schedules.
Restaurants
Key challenges: grease, food residues, strict hygiene standards, and mixed surfaces (stainless steel, tile, stone).
- Kitchen‑safe sanitization: Employ food‑grade ingredients that meet regulatory requirements for prep stations and equipment.
- Degrease‑and‑sanitize combo: Combine surfactants and antimicrobial actives to handle both visible soils and microbial control in one step.
- Low‑foam rinsing: Optimize cleaning in high‑volume dish areas while avoiding residue build‑up on cookware.
Hospitality
Key challenges: varied room types, textile care, and guest safety.
- Textile‑friendly options: Choose milder, pH‑balanced solutions suitable for linens and upholstery pre‑treatment.
- Multi‑area performance: Ensure bathroom tile, mirrors, and hard‑floor surfaces can all be addressed by the same base formula.
- Housekeeping efficiency: Standardize on one product to reduce training complexity and speed room turnover.
Restoration
Key challenges: smoke residue, mold, flood soils, and insurance compliance.
- High‑power emulsifiers: Target embedded soot and odour-causing particles from fire damage.
- Mildew control: Integrate antifungal additives that inhibit mold regrowth on damp surfaces.
- On‑site dilution stations: Facilitate mobile team deployments with ready‑to‑mix concentrates that adjust to water quality.
Manufacturing
Key challenges: industrial oils, production residues, and food‑grade sanitation.
- Heavy‑duty removal: Leverage chelating agents to break down metalworking fluids and process greases.
- Rinse‑safe for food zones: Confirm NSF‑certified ingredients where equipment contacts consumables.
- Non‑corrosive formula: Protect machinery and metal surfaces from etching or pitting over repeated cleanings.
Putting It All Together: Best Practices
- Train your team on proper dilution ratios, contact times, and application methods.
- Rotate sample patches when introducing a new cleaner—test small areas to verify compatibility.
- Monitor outcomes through checklists and spot audits, tracking both cleanliness and resource use.
- Adjust frequency based on foot traffic, seasonal demands, and regulatory updates.
By understanding each industry’s unique demands and standardizing around an eco‑friendly, versatile cleaner, operations can cut down on clutter, improve safety, and drive consistent results, without the headache of juggling dozens of specialty products.